凸轮分割器典型工程应用
凸轮分割器作为自动机械核心部件,大量使用在各种自动化装配专机、自动化生产线上。主要的应用类型为:
- 转盘式多工位自动化装配专机
- 与皮带或链条组成直线方向间歇输送的自动化生产线
- 自动化间歇送料机构(如冲床自动送料机构)
- 摆动机械手
下面分别举例进行说明:
1.转盘式多工位自动化专机
在凸轮分割器的基础上,只要再完成以下工作就可以组成一台完整的自动化装配专机:
- ①在凸轮分割器的输出轴上设计安装转盘;
- ②在转盘上设计安装特定的定位夹具;
- ③在转盘各工位上方(或转盘外侧)设置各种执行机构(如机械加工、铆接、焊接、装配、标示等装置);
- ④在需要添加零件的工位附近设置自动上料装置(如振盘、机械手等);
- ⑤在卸料工位设置自动卸料装置(如机械手等);
- ⑥设计传感器及PLC控制系统。
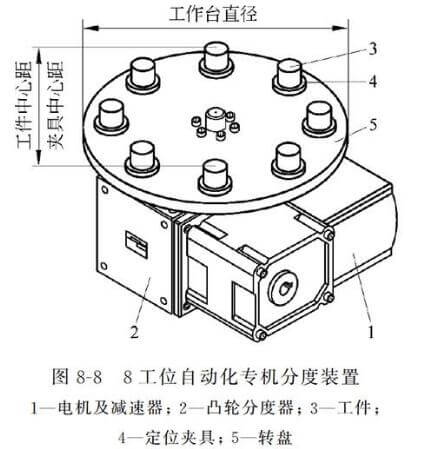
图8-8即为采用凸轮分割器的8工位转盘式自动化专机分度装置,电机经过减速器后直接驱动凸轮分割器的输入轴,而转盘则安装固定在凸轮分割器的输出轴上,结构紧凑,安装方便。为了更清楚地说明凸轮分割器的作用,图中未画出各工位对应的执行机构及自动上下料装置。
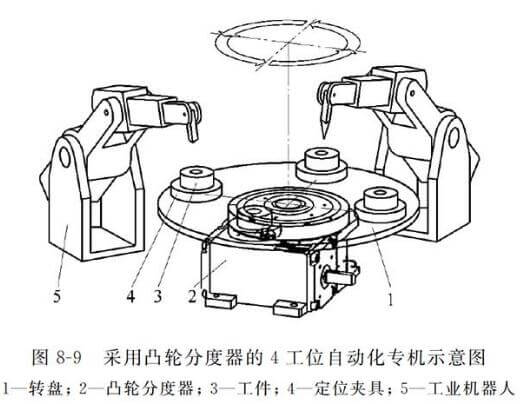
图8-9为采用凸轮分割器的4工位自动化专机示意图,图中在两个工位.上分别有两台作为装配执行机构的工业机器人,读者从中可以进一步理解此类自动化专机的组成原理。
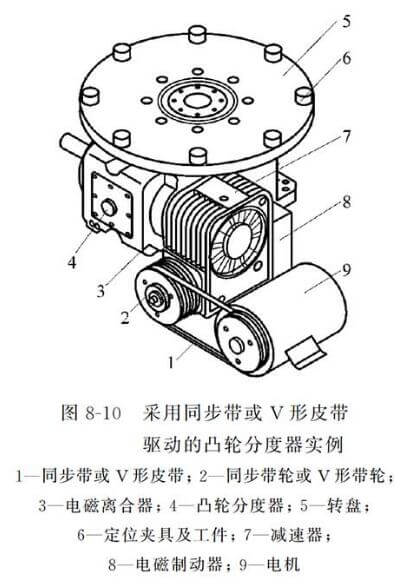
图8-10为采用凸轮分割器的8工位自动化专机分度装置示意图,电机通过皮带(同步带或V形皮带)及皮带轮驱动减速器,减速器再与凸轮分割器输人轴连接在一起。这样可以很灵活地设计凸轮分割器输入轴的转速,更方便地调整凸轮分割器的节拍时间。
读者在学习完本章后面关于节拍分析的内容后就会明白,输入轴的转速与凸轮分割器的节拍时间是相对应的,正是输人轴的转速决定了凸轮分割器的节拍时间。
在上述实例中,专机的工位数是根据产品的装配工序数量来选定的,工位,上方的执行机构也是根据产品的装配工艺专门设计的,定位夹具则是根据产品或零件的形状、尺寸专门设计的,自动上下料装置也是根据产品或零件的形状、尺寸专门设计的。
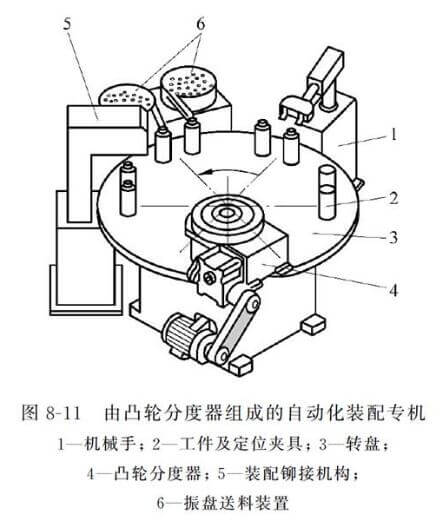
为了更清楚地看出如何用凸轮分割器组成自动化装配专机,下面用图8-11所示的例子来说明。在图8-11 中,凸轮分割器采用同步带传动,因此机器的工作节拍可以很方便地调整。在产品的装配过程中,既采用了机械手1作为自动上料机构,也采用了振盘6对某零件自动上料,作为执行机构的铆接机构5设置在转盘铆接工位的正上方。在工位的设计上,一个工位设计两套定位夹具,每次同时对两个产品进行装配,因此将机器的生产效率提高了一倍。
在某些生产场合需要极高的生产效率,需要将工位数设计得很大。例如大型的啤酒、饮料灌装专机为了提高生产效率目前已经将工位数提高到190个左右。又例如在某些电器部件的大型多工位热风软钎焊专机上,由于焊接部位要完成焊接需要有预热、焊接、保温、冷却等过程,工件在转盘上方的热风温度场中需要停留的时间较长,因此,一方面机器的工位数多达数十个,另–方面机器转盘的直径也很大,转盘的质量也会很大。
转盘的直径越大,转盘的质量也越大,给凸轮分割器的负载阻力就越大,要驱动转盘转动就需要更大的驱动扭矩。过大的负载施加在凸轮分割器上显然是不利的,为了尽可能减小凸轮分割器的负载,在这种场合一般都采用中空的转盘,以减轻转盘的质量。图8-12为采用大直径中空转盘的回转分度装置实例。
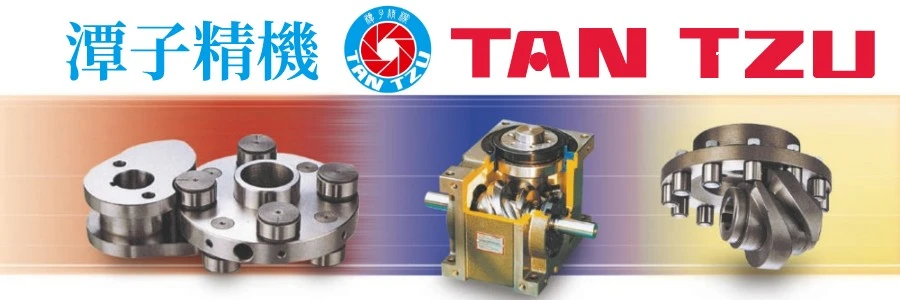