材料工程的最新进展为齿轮材料提供了替代方案。
齿轮是现代机械的常见部件,存在于齿轮箱、手表、电机、熔炉和自动化设备中。由于易于制造和可用的合金种类繁多,金属合金是齿轮最常用的材料。然而,也有其他选择:陶瓷和金属注射成型具有更高的强度和其他性能,使它们成为理想的选择。
金属合金和齿轮设计
齿轮使用的材料取决于强度和使用条件。使用条件的示例包括磨损和噪音。铸铁是一种常见的齿轮材料,因为它具有良好的耐磨性能、可加工性以及易于通过金属铸造生产复杂形状。蜗轮蜗杆倾向于使用磷青铜,因为该材料具有耐磨性。碳钢或合金钢因其高强度值而常用。这些钢经过热处理,以实现韧性和齿硬度的适当组合。
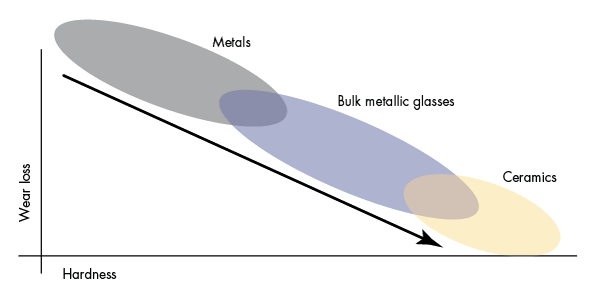
这三种材料的硬度范围如上图所示。块状金属玻璃位于金属和陶瓷的中间,因为金属最适合严重磨损,而陶瓷最适合最大硬度。
而硬度是齿轮设计中的一个重要因素:材料的硬度越高,所用齿轮的尺寸和重量就越能减小。例如,让我们比较两组齿轮组,其中第一组的布氏硬度数 (BHN) 为 2,000 N/mm2,第二组的 BHN 为 6,000 N/mm2。由于第二组的硬度更高,齿轮组更小,设计更紧凑。第二组的重量仅为第一组的 1/8,同时仍提供相同的功率。
硬度越高也表明表面耐久性或耐磨强度。表面耐久性越高,其抵抗齿面失效或“点蚀”的能力就越强,例如,由接触应力引起的疲劳。表面耐久性是抗压强度的函数,与硬度成正比。表面淬火通常通过表面硬化工艺实现:在齿轮表面产生坚硬的外壳,但使核心保持柔软。这样做,而不是通过硬化,因为增加硬度会导致材料更脆。
硬度值的一些例子是铸铁等级 35 的 BHN 最小值为 300 N/mm2。磷青铜离心铸件的 BHN 为 90 N/mm2。AISI 9310 是一种 300°F 的表面硬化钢合金,用于承受高负载和以高螺距线速度运行的航空航天齿轮。AISI 9310 的 BHN 值为 250 至 350 N/mm2。
陶瓷和金属注射齿轮
在选择齿轮的替代材料时,陶瓷和金属注射材料已成为流行的选择。原因很简单,对于需要高度耐磨的小尺寸应用,陶瓷和金属注射件可以大批量生产,并且比典型的钢合金更容易生产。
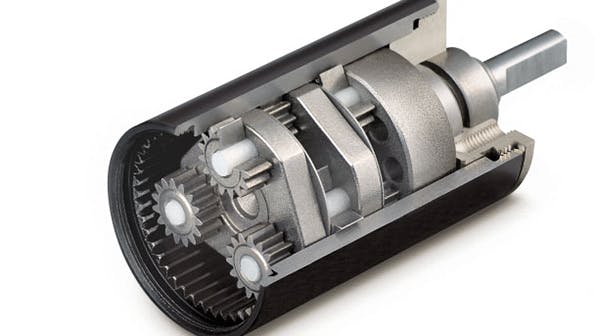
Maxon Motors的上述齿轮箱采用陶瓷轴,与金属合金相比,其最大连续扭矩为0.5至2.0 Nm,使用寿命更长。
这两种材料都是通过注塑成型工艺制成的。制备陶瓷和金属粉末作为原料。氧化锆 (ZrO2) 是一种用于注射工艺的常见陶瓷。对于金属粉末,用户可以制备他们想要的合金组合物混合物。一个例子是铁、铜、镍和钼(FeCr19Ni9Mo2)的 316L 混合物,用于其综合强度和耐腐蚀性。氧化铝(AlO2)是另一种常见的金属粉末。
蜡和聚合物结合添加剂用陶瓷和金属粉末加热。冷却后,它们被加工成颗粒状颗粒作为原料。然后,粉末在注塑机上加工。注塑成型件称为绿色压块。一旦离开机器,绿色粉饼就会被拆包。除胶从绿色压块中提取粘合材料。
下一步是将零件放入熔炉中进行烧结。烧结将压块加热到高温,以完成合金化和冶金键的形成。在烧结过程中会发生收缩,根据材料的不同,收缩率可能高达 30%。金属注射成型 (MIM) 的烧结温度约为 1,300°C,陶瓷注射成型 (CIM) 的烧结温度约为 1,500°C。可能需要对零件进行返工以达到所需的形状。使用经典的金属加工工艺,陶瓷部件使用金刚石工具。
陶瓷:优点和缺点
陶瓷在传统上金属合金会失效的应用中表现出色,例如,需要非磁性部件的条件,如真空或医疗应用。磨损优化是陶瓷理想的另一个条件。金属合金在磨损过程中往往会分解(磨损)。氧化锆的硬度为 1,200 维氏 (HV) 或更大。将其转换为 BHN 可提供 1140 N/mm2 的硬度。氧化锆的抗弯强度大于800 N/mm2,热膨胀系数为10 x10-6 °C-1。
与合金钢相比,氧化锆具有耐磨性和耐热性。相比之下,钢合金的热膨胀系数范围在 11 至 13 x 10-6 °C-1 之间。该值越低,扩展的可能性越小。陶瓷也是非磁性和生物相容性的。这使得它们非常适合生物技术和真空环境。陶瓷具有良好的隔电和耐热性,并具有抗摩擦性能。
不幸的是,陶瓷的断裂韧性较低,典型值小于 1 MPa*m1/2。它们的高熔点在铸造时会产生一些复杂性。陶瓷的最终成型过程也很昂贵。由于使用金刚石工具,如果需要任何精加工工作,陶瓷的成本可能会上升。陶瓷部件的尺寸也会影响成本。当零件体积小且数量大时,陶瓷效果最佳。大零件或短时间的零件并不能抵消制造成本。
金属注射成型:优点和缺点
MIM技术可以制造出形状复杂的大型钢制零件。可以生产螺纹和翅片等复杂特征,通常不需要二次加工工艺。成型工艺可生产出几乎不需要返工的高表面质量零件。材料特性与铸钢或轧钢非常相似。例如,MIM零件的密度是同类钢零件的96%至98%。例如,外科不锈钢是使用最广泛的MIM合金之一。
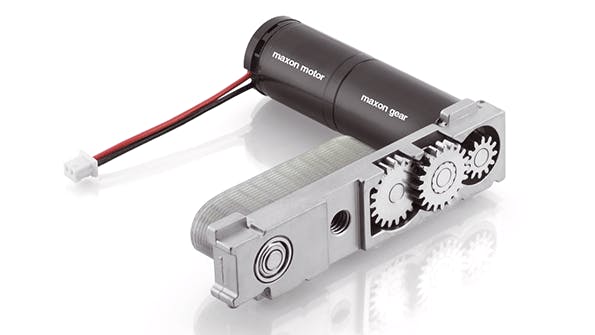
金属注射成型可以制造包括外壳和齿轮在内的零件,如上面Maxon Motors的电机组件所示。这有助于降低高度复杂零件的机器成本。
17-4 PH 成分 (AISI 630) 由铁、17% 铬、4% 镍、4% 铜和低含量的锰、硅和铌(或钽)组成。烧结和热处理至H1025后,屈服强度范围为965 MPa至1,040 MPa。与金属合金相比,MIM零件具有耐腐蚀性。MIM 部件能够替换整个组件,有助于减少所需的组件数量。例如,可以使用用于气门驱动的复合齿轮组来代替使用压制或焊接连接。
MIM具有与陶瓷类似的缺点。断裂韧性是在某些情况下可能很低,具体取决于材料。例如,V型缺口冲击试验表明,17-4 PH的断裂能仅为锻造材料的15%。制造的零件通常很小(10 毫米至 15 毫米)且数量很大。对于大零件和小批量来说,成本太高了。MIM的多步骤工艺也会导致昂贵的加工成本。初始成本和材料成本通常也很高。然而,额外的好处是,任何未使用的材料都可以回收以备将来使用,从而实现 100% 的材料使用。
金属玻璃作为未来的替代品
替代齿轮材料的未来可能取决于块状金属玻璃(BMG)的产生。BMG是一种设计的化合物,可以具有陶瓷和结晶金属的综合机械性能。与陶瓷类似,BMG具有高强度和耐磨性,但熔化温度较低。较低的温度将有助于零件的制造,而陶瓷和MIM的初始成本往往很高。其非结晶非晶态结构使其与钢一样坚固,但又像塑料一样具有延展性。BMG还具有耐腐蚀性,并具有高断裂韧性的潜力。
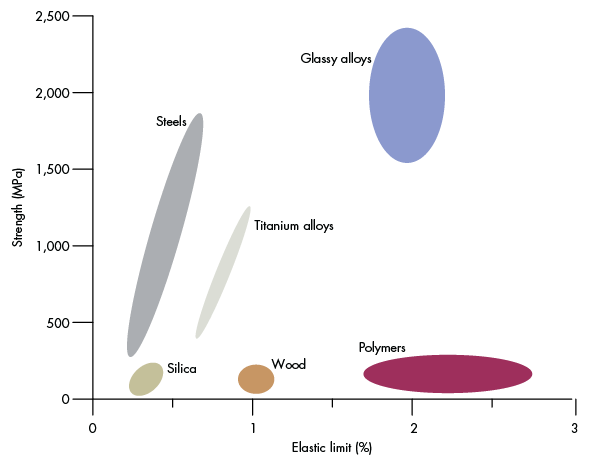
加州理工学院的威廉·约翰逊(William Johnson)提供的图表突出显示了某些材料与典型拉伸强度相比的弹性极限。
困扰金属、陶瓷和MIM零件的问题是它们的脆性,抗疲劳性差。然而,在BMG的情况下,导致裂纹轮廓的剪切带塑性有助于提高抗疲劳性。在BMG材料中,剪切带很容易形成,产生像齿轮齿一样互锁的裂纹。这些齿有助于限制裂缝的打开和闭合。BMG中的高体积剪切刚度比抵消了玻璃材料的脆性,因为形成剪切带所需的能量低于将它们转化为材料裂纹所需的能量。
伯克利实验室材料科学部的材料科学家罗伯特·里奇(Robert Ritchie)表示:“多重剪切带的影响是多方面的。剪切带的形成导致广泛的裂纹尖端钝化,从而导致内在增韧,而由此产生的裂纹挠度和闭合导致裂纹尖端屏蔽,从而导致外在增韧。
Richie和加州理工学院(California Institute of Technology)的教授威廉·约翰逊(William Johnson)共同研究了块状金属玻璃的制造。在接受Nature Materials采访时,Johnson继续描述了BMG生产的未来优势和当前障碍。目前,生产BMG所需的高加热和快速冷却是一个问题。压铸 BMG 需要超过 1,000°C 的热液体,然后快速冷却至玻璃化转变温度。
退火引起的脆化,紧随其后的是玻璃结晶,是金属玻璃生产中反复出现的问题,因为它阻碍了一致和均匀的制造。所需的高纯度材料,如纯氧化锆,推动了BMG的生产成本。
BMG生产的未来将依赖于使用替代原材料,如黑色金属(铁、镍和铬)来制造金属玻璃,并能够使用超冷变形而不是压铸。在过冷温度区域,金属玻璃的作用类似于热塑性塑料,更易于操作。