凸轮机构的加工精度和耐用性
提高凸轮机构的加工精度和耐用性可以通过以下几个方面来实现:
- 精密加工技术:采用高精度的加工设备和技术,如数控加工中心、精密磨床等,可以提高凸轮的加工精度。例如,四轴加工方法可用于加工圆柱凸轮,以获得较满意的效果。
- 合理选择材料:凸轮和从动件的材料选择对耐磨性和强度有重要影响。常用的凸轮材料有45号钢或40Cr钢,淬硬至52~58HRC,更高要求时可用15号钢或20Cr钢渗碳并淬火至56~62HRC。对于轻载凸轮,也可以使用优质灰铸铁或45号钢调质处理到22~26HRC。
- 热处理和表面处理:通过热处理如淬火、渗碳、氮化等方法提高凸轮表面的硬度和耐磨性。例如,氮化处理可以使表面硬度达到60~67HRC,增强凸轮表面的耐磨性。
- 精确的公差控制:在设计和加工过程中,严格控制凸轮的尺寸公差和形状公差,以确保凸轮机构的运动精度和可靠性。
- 润滑和维护:合理的润滑可以减少凸轮和从动件之间的摩擦和磨损,延长使用寿命。应选择适当的润滑油和润滑方式,并定期进行维护和检查。
- 优化设计:通过优化凸轮的形状和机构设计,减少接触应力,提高凸轮机构的传动效率和耐用性。例如,优化设计可以考虑凸轮的基圆半径、滚子型号和尺寸,以及从动件的支承方式等。
- 使用高质量的轴承和滚子:高质量的轴承和滚子可以承受更大的负载,减少磨损,提高凸轮机构的耐用性。
- 计算机辅助设计和分析:利用CAD/CAM软件进行凸轮机构的设计和分析,可以提高设计的准确性和加工的精度。
通过上述措施,可以有效提高凸轮机构的加工精度和耐用性,从而提高机械系统的整体性能和可靠性。

通过计算机辅助设计(CAD)提高凸轮机构的设计精度?
通过计算机辅助设计(CAD)提高凸轮机构的设计精度,可以采取以下措施:
- 精确建模:使用高精度的CAD软件,如AutoCAD Mechanical,进行凸轮机构的详细设计。这些软件提供了专门的凸轮设计工具,可以精确地创建和编辑凸轮的几何形状和轮廓曲线 。
- 参数化设计:利用CAD软件的参数化设计功能,可以快速调整凸轮的尺寸和形状参数,从而优化设计。这样,设计者可以轻松地修改凸轮的尺寸、偏距、厚度等,并立即看到这些变化如何影响整个机构 。
- 运动仿真:在CAD软件中进行运动仿真,以验证凸轮机构的运动是否符合设计要求。这有助于在实际制造之前发现潜在的问题,并进行必要的调整 。
- 优化设计:采用优化算法,如元启发式算法,可以在CAD环境中对凸轮机构进行多目标优化,以提高传动效率、减少接触应力和压力角等 。
- 数控(NC)数据生成:利用CAD软件生成精确的NC数据,以指导数控机床进行精确加工。这确保了凸轮机构的制造精度与设计精度相匹配 。
- 材料和力学性能分析:在设计过程中考虑材料选择和力学性能,使用CAD软件进行有限元分析(FEA),以确保凸轮机构在运行中的强度和耐久性。
- 专家系统和知识库:开发或使用现有的凸轮机构设计专家系统,这些系统通常包含丰富的设计规则和经验数据,可以帮助设计者做出更准确的决策 。
- 文档和标准:遵循行业标准和最佳实践,确保设计过程中的每一步都有文档记录,以便于审查和质量控制。
通过上述方法,CAD技术可以帮助设计者提高凸轮机构的设计精度,减少错误和返工,从而提高最终产品的质量和性能。
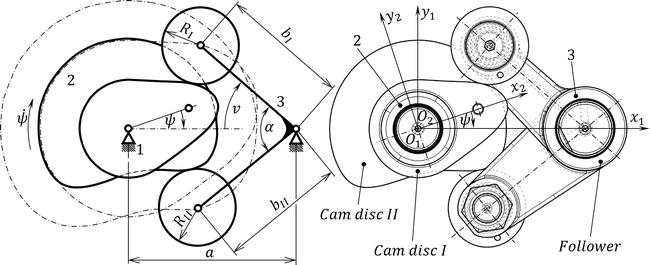
在热处理过程中,如何确保凸轮的硬度和耐磨性?
在热处理过程中,确保凸轮的硬度和耐磨性的关键参数包括:
- 材料选择:选择合适的材料是提高凸轮耐磨性和硬度的基础。常用的凸轮材料包括45、45Mn2、40Cr等优质结构碳素钢,以及GCr15轴承钢等 。
- 加热温度:凸轮需要被加热到适当的温度以改变其组织结构。加热温度必须精确控制,以确保凸轮轴达到所需的热处理效果 。
- 保温时间:在加热到一定温度后,凸轮需要保持在该温度一段时间,以确保材料内部组织的变化。
- 冷却速度:淬火过程中的冷却速度对硬度和耐磨性有显著影响。常用的淬火介质有水、油和气体等,选择合适的淬火介质和冷却速度是确保凸轮获得理想性能的关键 。
- 回火处理:淬火后的凸轮通常需要进行回火处理,以消除淬火应力,提高耐磨性和韧性。回火温度和时间的选择对凸轮的性能有重要影响 。
- 表面硬化处理:表面硬化处理如渗碳、氮化、感应淬火等,可以显著提高凸轮表面的硬度和耐磨性 。
- 硬化层深度:对于表面硬化处理的凸轮,硬化层的深度也是一个重要参数,它影响凸轮的耐磨性和使用寿命。
- 热处理后的精加工:热处理后,凸轮可能需要进行精磨或其他精加工工序,以确保最终的尺寸精度和表面光洁度。
- 质量控制:在整个热处理过程中,需要对上述参数进行严格的监控和质量控制,以确保凸轮的性能满足设计要求。
通过精确控制这些参数,可以显著提高凸轮的硬度和耐磨性,从而提高其在各种应用中的性能和寿命。
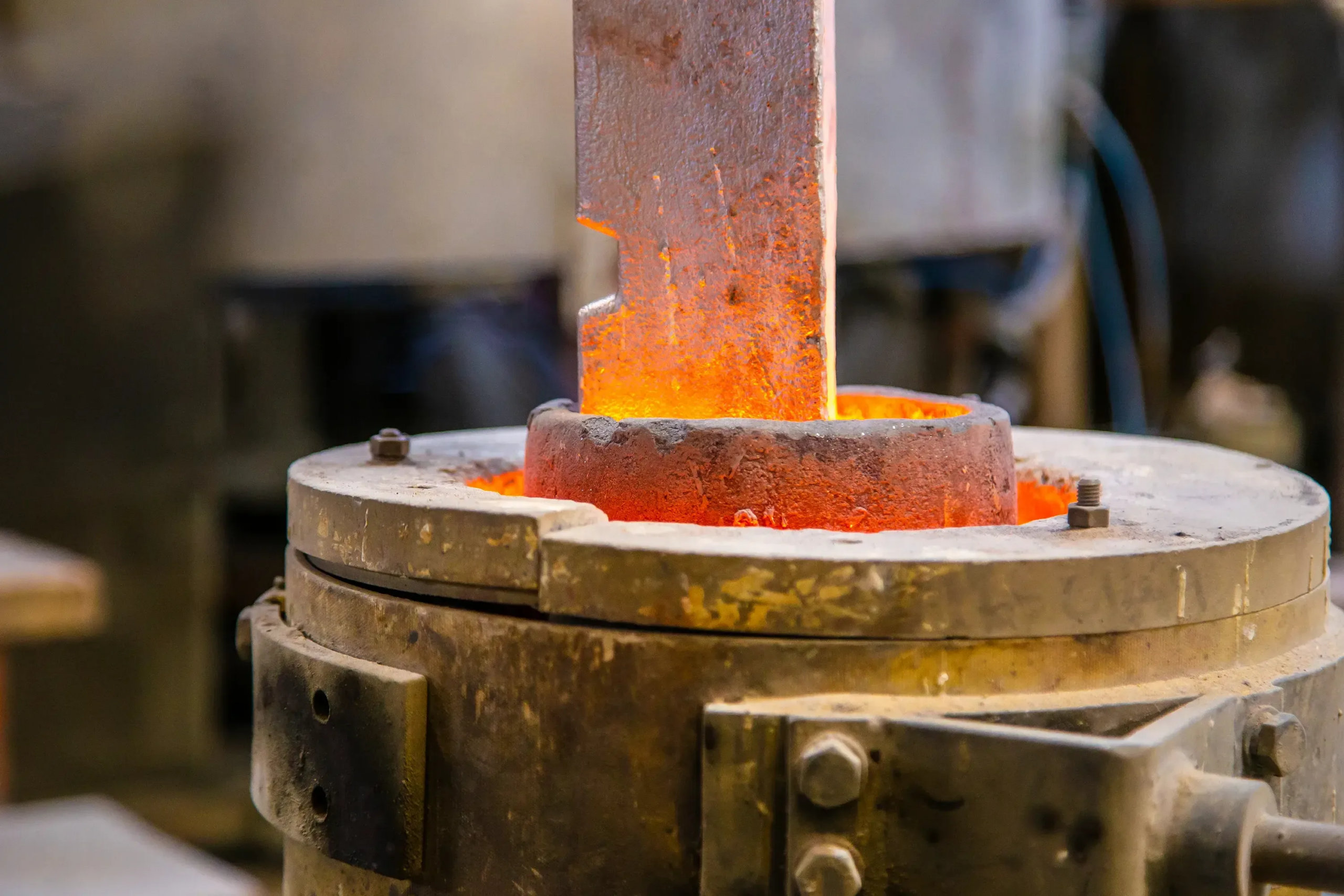