CNC 可能看起来很神奇。毕竟,工程师只需要设计一个零件,通过一些CAM软件发送,然后让CNC机器做它的事情并自动切割一个零件。但这并不完全正确。工程师需要注意 CNC 加工的限制。例如,即使在工具和 CNC 控制方面取得了所有进步,也不是工程师能想象到的所有形状和特征都可以创建出来。
以下是有关如何利用 CNC 的功能并避免其限制的一些建议。
公差
公差是零件尺寸的可接受范围或尺寸。它们是根据零件的形状、配合和功能确定的。工程师应该记住,由于废品率增加、额外的夹具和特殊的测量工具,更严格的公差会增加成本。由于检测时间的增加,严格的公差也增加了成本。根据设计人员要求的公差,与按照标准公差加工的成本相比,成本可能会增加一倍以上。只有当需要满足零件的设计标准时,才应使用更严格的公差。
更严格的公差也会延长 CNC 循环时间,因为 CNC 机器必须减速以保持更严格的公差。
如果工程师不向提供给 CNC 供应商的图纸、模型或规格表添加公差,他们可以遵循自己关于公差的一般规格。这些规格可能因公司而异。一些供应商公司没有默认的公差设置,并要求客户提供这些设置。
应用公差的最佳方法是仅对关键区域应用严格的几何公差,这将降低总体成本。
大小限制
对于铣削,零件尺寸受机器功能和所需零件特性的切削深度的限制。请记住,构建空间尺寸并不等同于零件尺寸。例如,Z 轴行程为 38 英寸。并不意味着零件可以加工到该深度或高度。根据零件的尺寸和需要加工的特征,零件的 Z 高度必须小于 38 英寸。以适应刀具间隙和切削深度。特性和零件尺寸决定了零件的可加工高度。
对于车床,零件尺寸取决于构建空间以及零件的直径和长度。CNC 供应商可能会提供带电工具车床。它可以大大缩短交货时间,但也可以通过在车床内提供 CNC 铣削功能来增加可以加工的特征的数量和类型。
材料选择
材料选择对于确定零件的整体功能和成本至关重要。 工程师必须定义最终零件的重要材料特性,包括硬度、刚度、耐化学性、热处理性和热稳定性,仅举几例。
进行 CNC 加工的材料通常以毛坯形式出现,而毛坯的尺寸限制了零件的尺寸。例如,如果成品零件的尺寸为 3.5 × 2 × 1 英寸,则材料毛坯尺寸至少需要为 3.75 × 2.125 × 1.125 英寸。原始形式的高大。在设计过程中应考虑材料毛坯厚度。
一个好的规则是使用至少 0.125 英寸的空白。比零件大。例如,如果最终尺寸为 1 × 1 × 1 英寸,则坯料应为 1.125 × 1.125 × 1.125 英寸。以允许空白大小的变化。在此示例中,如果工程师决定如果最终零件尺寸为 0.875 × 0.875 × 0.875 英寸,则零件的形状、配合和功能不会改变,则为标准 1 x 1 x 1 英寸。块可以使用。与从更大的毛坯开始相比,这降低了材料成本。
对于较软的金属,如铝和黄铜,以及塑料,与较硬的材料相比,加工时间通常更短,从而节省时间和金钱。那些较硬的材料,如不锈钢和碳钢,必须在较低的主轴转速和机床进给率下进行加工。例如,铝的加工速度通常比碳钢快四倍,比不锈钢快八倍。
所使用的材料是零件最终成本的主要组成部分。例如, 6061 铝棒材大约是每磅铝板价格的一半, 而 7075 铝棒材可以是 6061 棒材成本的两到三倍.304不锈钢的成本大约是6061铝的两到三倍,大约是1018碳钢的两倍。如果设计不能保证碳钢或不锈钢的性能,请考虑使用 6061 铝以最大程度地减少材料费用。
如果设计不需要金属的刚性,塑料通常是金属的更便宜的替代品。例如,聚乙烯易于加工,成本约为 6061 铝价格的三分之一。一般来说,ABS的成本约为缩醛的1.5倍;尼龙和聚碳酸酯的成本大约是乙缩醛的三倍。但是,塑料可能更难保持严格的公差,并且由于塑料被加工掉时产生的应力,零件在加工后可能会翘曲。
复杂性
零件越复杂,这意味着必须切割轮廓几何形状或多个面,由于额外的设置时间和切割零件的时间,其成本就越高。当一个零件可以在两个轴上切割时,可以更快地完成设置和加工,从而最大限度地降低成本。
对于简单的两轴零件,当工具在零件周围移动时,会去除更多的材料。对于更复杂的零件,需要使用 X、Y 和 Z 轴一起移动来切割某些区域。
为了创建具有良好表面光洁度的复杂表面,首选小切口。它增加了加工时间,因此零件的价格也会增加。为了最大限度地降低成本,设计时仅使用两轴切割。如果零件需要特定的外观或功能,则可能无法做到这一点。另一种节省成本的方法是保持一致,例如内部拐角半径和螺纹孔。这通过降低更换工具的需要来节省时间。
也许降低 CNC 加工复杂零件成本的最佳方法是使用五轴加工。五轴加工使切削刀具和零件可以同时围绕多达五个轴移动。这意味着刀具路径更高效,需要的设置更少。三轴加工通常需要复杂的夹具,这些夹具必须定制,以便将零件保持在创建特征所需的方向。具有五轴功能的机床还可以使切削刀具保持与切削表面的切向。因此,工具的每次通过都可以去除更多材料,并留下更好的表面光洁度。
圆角和底切
使用 CNC 立式或卧式铣床时,所有内部垂直墙都必须有一个半径。这是因为以高转速旋转的圆形工具正在去除材料。设计应考虑到此限制将产生半径的区域。
对于内角半径,最好使用非标准半径,因为在追踪内角时,立铣刀需要间隙才能转动和继续铣削。如果零件具有 0.25 英寸。在内半径内,标准立铣刀需要锤击拐角,完全停止,枢轴 90 度,然后继续切割。这会减慢加工速度,从而增加成本并引起振动。但只增加 0.02 到 0.05 英寸。(0.508 至 1.27 毫米)到内部半径,将让转弯而不会完全停止。这不仅可以降低成本,还可以提高成品CNC零件。
一般来说,半径越大,成本越低。这是因为可以使用更大的刀具,并且每次切割会去除更多的材料,从而减少加工时间。例如,具有 0.125 英寸的工具。直径大约是使用 0.187 英寸完成这项工作的 1.5 倍。直径工具,长度大约是使用 0.250 英寸的两倍。工具。
即使可以使用小半径工具(半径低至 0.015 英寸),但有时工具需要深入材料的深度使得无法切割小直径孔,因为该工具尚未在市场上买到。而且,如果刀具是定制的,加工成本将大大增加,因为它只能进行小的切割,从而延长了制造时间。
如果切削深度超过切削刀具直径的两倍,则需要降低刀具的进给率,从而导致循环时间和成本增加。切割深度每增加一倍,进给率就会减半以上,从而使切割特征的时间增加一倍以上。最大切削深度与刀具直径之比为六倍;除此之外,还必须订购特殊工具。例如,如果 0.125 英寸。使用直径工具时,最深的切割深度应为0.750英寸。在必须使用自定义工具之前。
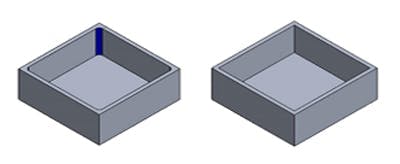
在创建与拐角相接的地板半径时,如果地板半径小于拐角半径,则加工要容易得多。使用现代CAD系统,使计算机生成相同尺寸的地板和墙壁半径非常简单。然而,这使得去除角落里的材料变得困难。如果地板半径小于垂直墙面半径,则同一工具可以去除材料并在拐角处形成顺畅的流动。
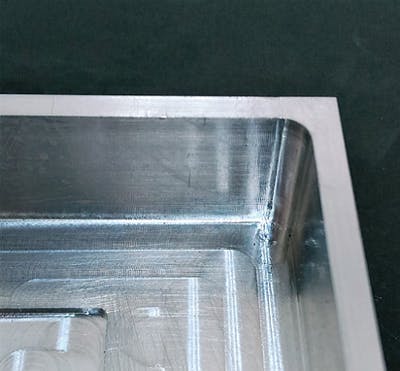
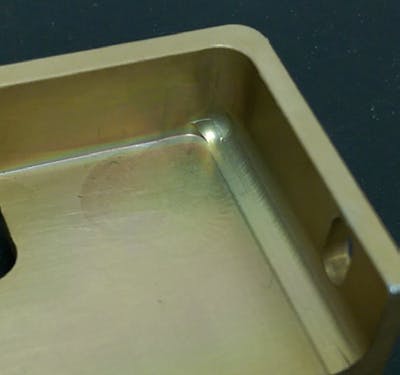
工程师有时会在标准加工工具无法到达的区域设计特征,从而在零件上形成底切区域。
由于几个原因,在设计底切时必须小心。首先,如果特征不是标准尺寸,则底切可能需要创建特殊工具。在下面的示例中,插槽中的半径为 0.053 英寸。创建几何形状需要昂贵的定制工具,这将大大增加零件的成本,尤其是在只制造几个零件的情况下。如果是标准的 0.062 英寸。使用 Radius,但是,该工具的成本将不到定制工具成本的一半。
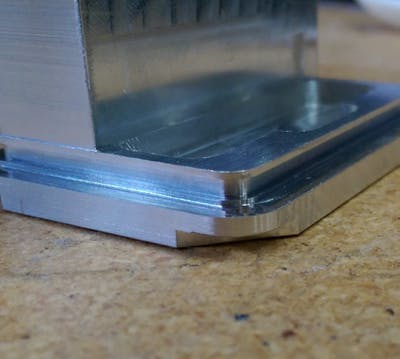
在设计底切时要小心的第二个原因是确保底切不会太深或无法触及。由于所需的工具具有连接到垂直轴的水平切割刀片,因此它限制了其切割深度。对底切的深度没有硬性规定,但底切越浅越好。此外,在设计底切特征时,仅在工具可以触及的区域创建底切。
有几种方法可以在零件中创建螺纹,包括切割丝锥、成型丝锥和螺纹铣刀。这些都是有效的方法,但设计工程师应牢记以下几点:
- 始终选择设计允许的最大螺纹尺寸,因为它简化了制造过程。水龙头越小,水龙头在生产过程中破裂的可能性就越大。
- 仅线程到所需的长度。由于可能需要专门的工具来满足深度要求,因此深螺纹孔会增加零件的成本。
- 尝试使用现成的螺纹尺寸以节省成本。